As we all know, some of the problems we often encounter in the production process of copper wire are nothing more than the outer diameter deviation of the product, the oxidation problem of copper wire in the wire drawing process, and the problem of short wire.
This is also a common problem that troubles many front-line technical workers. Because this directly affects their efficiency in the production process. The boss gives us such a high salary, but we don’t create greater value. For many technical workers, there is some embarrassment and apology. For many people in charge of the cable industry of many companies, workers often encounter various problems in the production process, which not only affects the efficiency of the entire production, but also poses a great obstacle to the performance evaluation of workers. So, today, I will talk to you about a series of common problems we will encounter in the production process. First of all, the first problem is that we will encounter a deviation in the wire diameter of copper wire drawing during the production process. So, why does this problem occur? What causes the deviation in the wire diameter of the wire drawing?
We know that due to the continuous production process of our copper wire drawing machine and annealing machine equipment, the speed of the drawing part will be inconsistent with the annealing part, that is, there will be a phenomenon of asynchrony, and this will directly lead to intermittent and irregular changes in the wire diameter due to the different speeds of the traction part during copper wire drawing. I have summarized the reasons, which are mainly due to the following points: First, the instability of the tension on the tension frame. We know that most of our workshops share one air pump, or multiple equipment share one air pump. Then, the air pressure of the air pump will be unstable, sometimes large, sometimes small, sometimes high, and sometimes low. As a result, the tension on the tension frame is unstable. However, because the speed of the wire collection during the wire drawing process is stable and unchanged, the force presented in the copper wire drawing process is also uneven, which will cause a deviation in the outer diameter of the copper wire drawing and cannot be accurately controlled. Second, the shaking of the copper wire on the annealing wheel. This is because the copper material and the copper wire are not uniformly stretched and relaxed during the annealing process, and the current density of our annealing machine is also unstable, which causes the spark effect on the surface of our copper wire during the wire drawing process due to vibration, and finally leads to uneven wire diameter.
Third, the wear of the gear box of the main motor during long-term production and use
In the long run, the speed of the fixed speed wheel of the wire drawing main machine will be inconsistent with the speed of traction, causing disharmony, and finally leading to uneven or thinning of the copper wire.
Okay, I just talked about several reasons that cause the copper wire to be uneven and the accuracy to be reduced during the production process of the copper wire drawing equipment. Then let me tell you how to solve it and how to avoid it?
My suggestion is to break them down one by one, and solve them one by one. From the first point, if the tension frame is unstable, then we can maintain the tension frame and lubricate the related moving parts frequently to avoid the incoordination of our tension frame during the wire drawing process when it is running at a high speed, and the friction will eventually make our wire uneven. In addition, we need to adjust the strength of the tension frame so that the copper wire is always close to the annealing wheel during the wire drawing process, so as to ensure that our annealing wheel will not cause sparks generated by vibration or defects on the surface of the annealing wheel due to friction, which will eventually lead to instability of the annealing current.
In addition, we need to make a wire drawing die according to the actual configuration of our copper wire drawing machine, and pay attention to the slip coefficient of wire drawing, which is a very important point in our wire drawing die matching process.
The above points hope to solve some related problems for you. In the future, I will share with you some problems and solutions that are often encountered in the production process of copper wire drawing machines.
If there is anything you don’t understand, or you have doubts about my analysis, you are very welcome to raise it with friends in the industry, or talk to me, discuss together, and make progress together
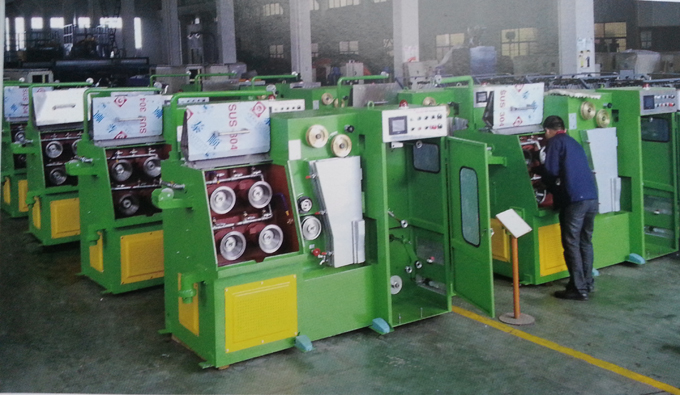